A Comprehensive Guide to the Refine and Advantages of Plastic Extrusion
In the large realm of manufacturing, plastic extrusion arises as a necessary and very efficient process. Altering raw plastic into continual accounts, it deals with a huge selection of industries with its exceptional adaptability. This guide aims to clarify the detailed actions associated with this method, the sorts of plastic suitable for extrusion, and the game-changing advantages it brings to the sector. The taking place conversation promises to unravel the real-world impacts of this transformative process.
Recognizing the Fundamentals of Plastic Extrusion
While it might show up complicated in the beginning glance, the process of plastic extrusion is basically basic - plastic extrusion. It is a high-volume production strategy in which raw plastic is thawed and shaped into a constant account. The procedure begins with the feeding of plastic material, in the form of pellets, granules, or powders, into a heated barrel. The plastic is then thawed utilizing a mix of warmth and shear, used by a revolving screw. When the molten plastic reaches completion of the barrel, it is required via a tiny opening recognized as a die, forming it into a desired kind. The designed plastic is after that cooled down, strengthened, and reduced into preferred lengths, finishing the procedure.
The Technical Refine of Plastic Extrusion Explained
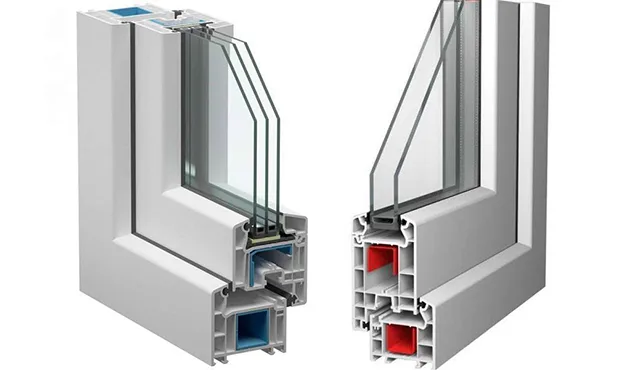
Sorts Of Plastic Suitable for Extrusion
The selection of the appropriate type of plastic is an essential aspect of the extrusion procedure. Numerous plastics provide unique residential or commercial properties, making them more matched to specific applications. Recognizing these plastic kinds can considerably boost the extrusion process.
Comparing Plastic Extrusion to Other Plastic Forming Approaches
Recognizing the kinds of plastic appropriate for extrusion leads the method for a wider conversation on just how plastic extrusion piles up against other plastic developing techniques. Plastic extrusion is exceptional when it comes to developing continuous profiles, such as gaskets, seals, and pipes. It also enables for a regular cross-section along the size of the product.
Trick Benefits of Plastic Extrusion in Production
In the world of production, plastic extrusion provides many significant benefits. One notable advantage is the cost-effectiveness of the process, which makes it a financially enticing manufacturing approach. Additionally, this strategy offers superior product adaptability and improved production rate, consequently raising total production effectiveness.
Cost-Effective Production Approach
Plastic extrusion jumps to the center as a cost-effective manufacturing method in manufacturing. This process stands apart for its capacity to create high quantities of material swiftly and effectively, supplying manufacturers with substantial cost savings. The primary price benefit is the ability to utilize More about the author less expensive basic materials. Extrusion utilizes polycarbonate products, which are less expensive contrasted to ceramics or steels. Even more, the extrusion procedure itself is fairly simple, minimizing labor prices. Additionally, plastic extrusion calls for less energy than see standard manufacturing approaches, contributing to lower functional costs. The procedure additionally minimizes waste, as any type of faulty or excess products can be reused and reused, giving another layer of cost-effectiveness. In general, the economic advantages make plastic extrusion a highly appealing option in the manufacturing market.
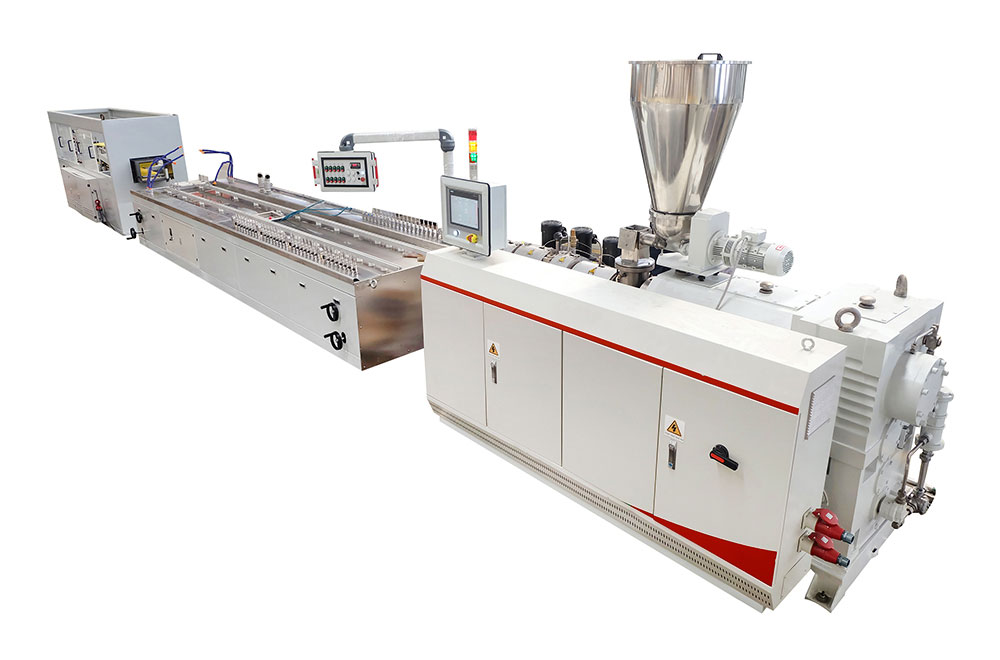
Superior Product Versatility
Past the cost-effectiveness of plastic extrusion, one more substantial advantage in manufacturing lies in its premium product versatility. This makes plastic extrusion a perfect remedy for markets that call for customized plastic elements, such as auto, building and construction, and packaging. In essence, plastic extrusion's item adaptability cultivates development while enhancing operational performance.
Improved Manufacturing Rate
A considerable advantage of plastic extrusion exists in its boosted manufacturing speed. Few other manufacturing processes can match the rate of plastic extrusion. In addition, the capacity to keep constant high-speed manufacturing without compromising product high quality sets plastic extrusion apart from various other techniques.
Real-world Applications and Influences of Plastic Extrusion
In the world of production, the technique of plastic extrusion holds profound importance. The economic benefit of plastic extrusion, primarily its economical and high-volume outcome, has actually revolutionized manufacturing. The industry is persistently making every effort for developments in eco-friendly and recyclable products, showing a future where the benefits of plastic extrusion can be retained without compromising ecological sustainability.
Final thought
Finally, plastic extrusion is a efficient and very reliable approach of changing basic materials right into varied products. It provides various advantages over other plastic developing approaches, including cost-effectiveness, high outcome, minimal waste, and design flexibility. Its influence is profoundly really felt in different markets such as construction, auto, and customer items, making it an essential find process in today's production landscape.
Digging deeper right into the technological procedure of plastic extrusion, it starts with the choice of the suitable plastic material. As soon as cooled down, the plastic is reduced into the called for lengths or wound onto reels if the item is a plastic film or sheet - plastic extrusion. Contrasting Plastic Extrusion to Various Other Plastic Forming Techniques
Recognizing the types of plastic suitable for extrusion leads the means for a more comprehensive discussion on how plastic extrusion piles up versus other plastic forming approaches. Few other manufacturing procedures can match the rate of plastic extrusion.